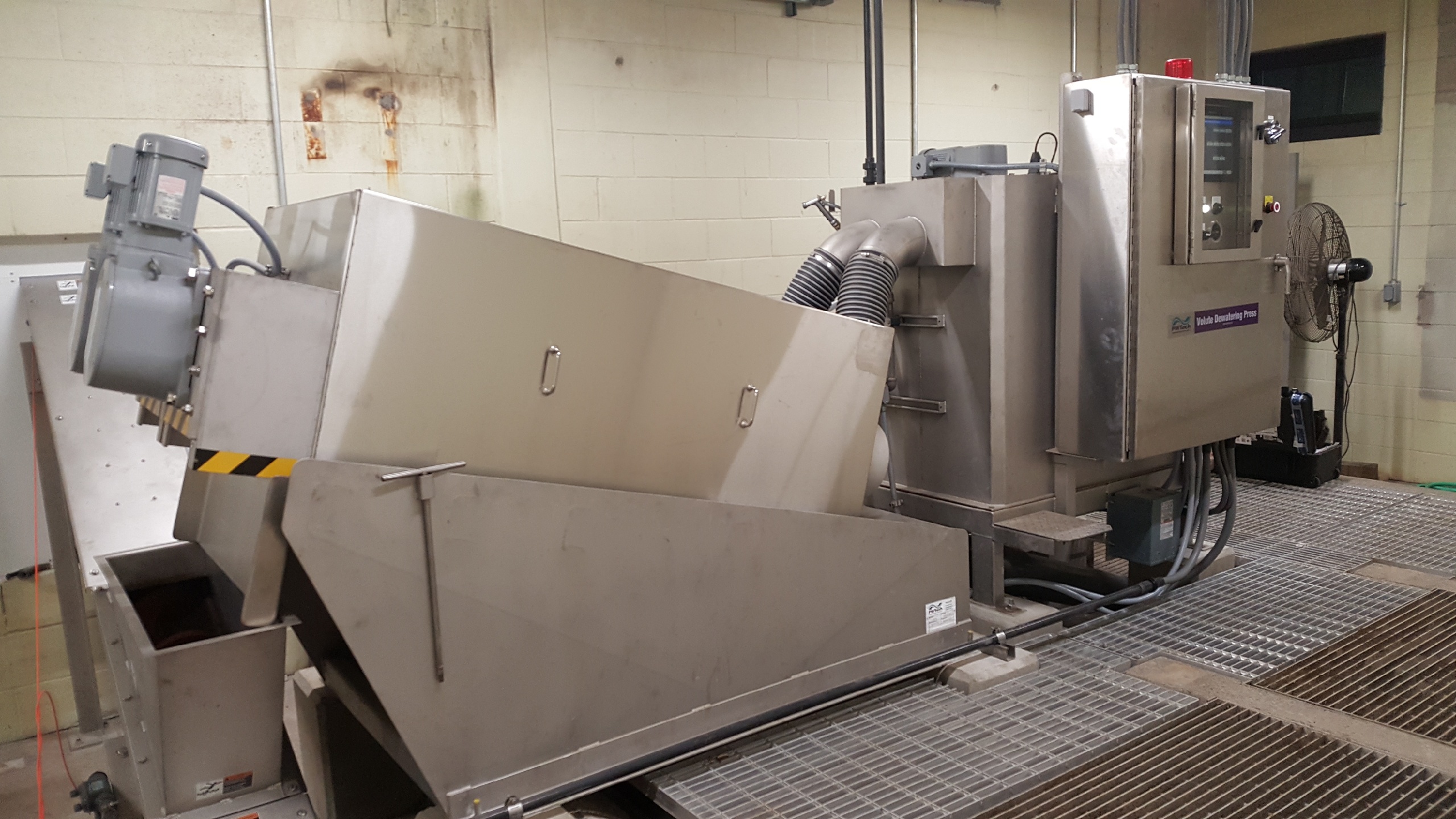
Bellows Falls Wastewater Treatment Plant Cut Costs and Improved Sustainability with Sludge Dewatering Press and Dryer
Bellows Falls Wastewater Treatment Plant in USA
- Sludge dewatering press
- Sewage treatment
- Operating cost reduction
- Industrial waste disposal cost reduction
- Operation management man-hour reduction
- Maintenance man-hours reduction
- Bellows Falls Wastewater Treatment Plant in USA
Our partner in USA, Process Wastewater Technologies, LLC helps Vermont wastewater treatment plant cut hauling costs by 75% and greatly enhance sustainability with an advanced dewatering and drying process.
HIGHLIGHTS
- Increased solids from 18-22% to around 90%
- Reduced solids production by 75%
- Eliminated landfill disposal and related trucking impacts
- Achieved a Class A biosolid approved for farmland application
- Estimated ROI of less than 5 years
Bellows Falls Wastewater Treatment Plant in Bellows Falls, VT, processes 0.5MGD of flow, plus about 2.2MGY of residential septage and light industrial waste that runs through a methane-heated anaerobic digester. Located near the Vermont/New Hampshire border, the plant serves the mostly rural residents of Bellows Falls, a town of about 2,800 people located along the Connecticut River.
Problem
Belt filter press required significant maintenance and labor and produced a very wet sludge
The plant was using a belt filter press that processed sludge to a consistency of 18-22% solids, at which point the plant trucked the cake to a compost facility 20 miles away in New Hampshire. With trucking fees, landfill disposal costs and related environmental impacts, as well as the labor and maintenance demands of the belt filter press, the plant knew there had to be a better way. To make matters worse, the New Hampshire compost facility became unavailable, which meant that sludge would need to be trucked 130 miles to Vermont’s only landfill.
- Significant labor and maintenance costs
- Sludge with a low solid density
- High trucking and landfill fees
- Undesired environmental impacts
Solution
VOLUTE™ Dewatering Press plus electric dryer removes much more water, with automation and low maintenance
After seriously considering a fan press, plant operators became aware of a different kind of technology – a dewatering screw press, which just happened to have a pilot unit in the area. Following a successful pilot of the VOLUTE™ technology and an evaluated bid process, in 2017 the plant became the first in Vermont to install a VOLUTE™ Dewatering Press, at about the time that the New Hampshire compost facility was no longer available. While the screw press greatly improved solids to a cake of 27-30%, the plant decided to go further, to reduce trucking and landfill costs, as it was now contending with a 130-mile trip to the landfill, per truck. In 2020, electric dryer technology was added to the process to produce a cake of 82-90% solids, which meets Vermont and New Hampshire state standards for farmland application.
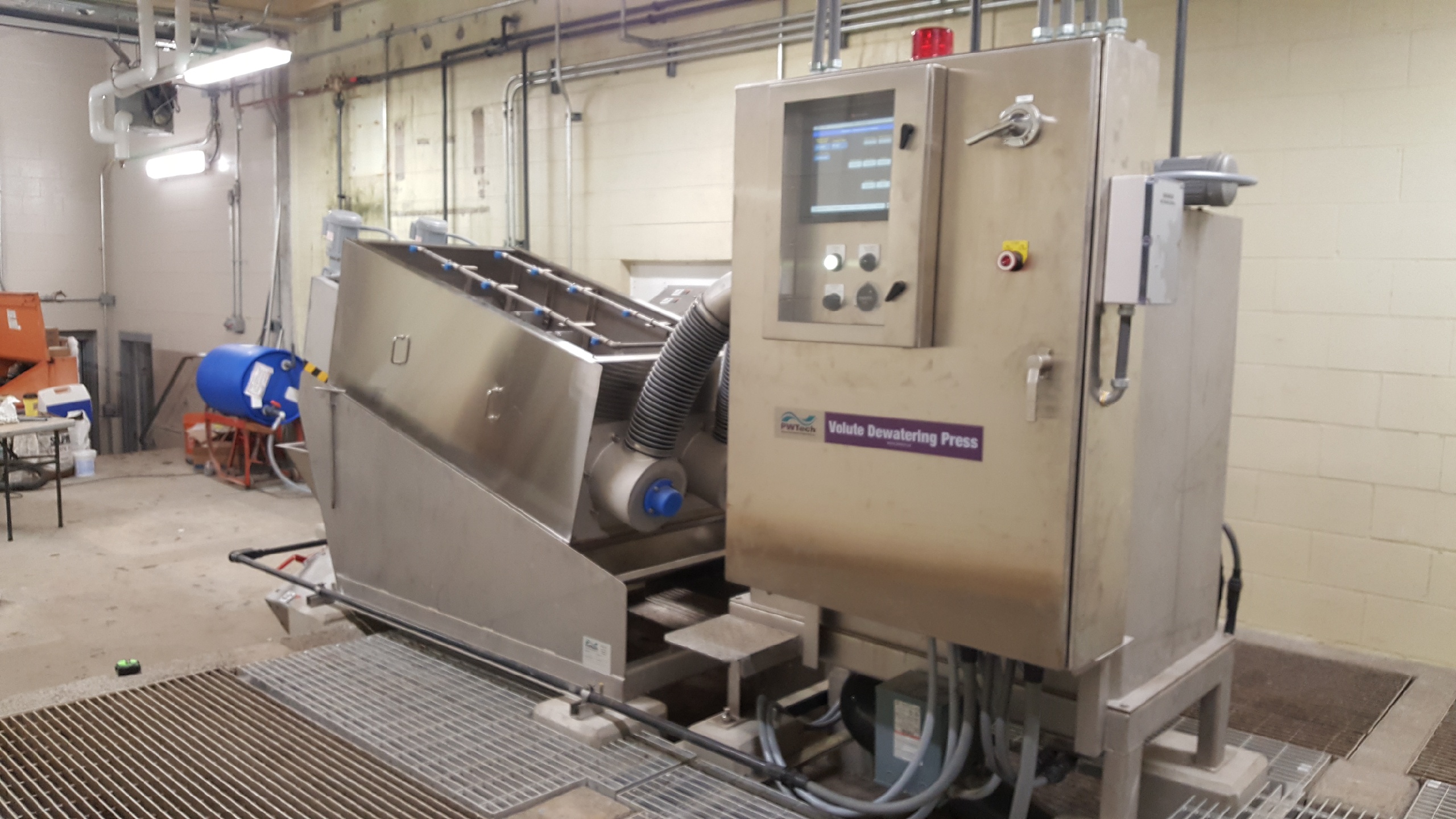
This process overhaul has resulted in a significant reduction in solids handling – the plant has reduced its output by more than 75%, thanks to the more effective removal of water. Implications include savings on landfill fees and trucking costs – now producing just one 30-yard dumpster per month as compared to four dumpsters previously. The final product is a Class A biosolid that is picked up in 1-ton super sacks by local farmers, further enhancing cost savings compared to prior disposal methods and virtually eliminating landfill fees, trucking costs and related environmental impacts.
Like a traditional belt press, The VOLUTE™ Dewatering Press uses a polymer to flocculate the solids and then squeeze them to create a semi-dry cake. But while the belt press sends the solids through multiple rollers fitted with filter belts, the screw press sends the solids very slowly through a dewatering drum using an auger, in a process that uses less energy and requires much less maintenance. The dewatering drum is a combination of fixed and moving rings around a screw auger, and can achieve both thickening and dewatering of the feed sludge. It’s ideal equipment for feeding into the dryer, both due to its slow and steady speed and unattended operation.
Additionally, the screw press requires much less wash water than the belt filter press, which depended on a constant stream of water to operate (the screw press uses water only as needed for periodic rinsing). The upgraded system at Bellows Falls WWTP operates about eight hours per day, five days per week, reliably and without supervision. Plant operators like the fact that the only regular maintenance is conducted on the mixing paddles, which require cleaning no more than once a month due to a lack of screening for the plant. In addition, ring cartridges at the end of the process are the only “wear” item and easy to replace, although this has not yet been required during the first five years of operation. Added in 2020, the dryer operates at 10 GPM, eight hours per day, using about 600 kWh per day. The dryer consistently reduces volume by 60% to 80%, with dry solids frequently reaching concentrations of greater than 90%. The interior system temperature of the dryer is 70 to 75 degrees C, and the machine uses three to five times less energy than competing sludge dryers. Due to its design, the dryer does not require odor control, dust suppression or explosion proof ratings.
Results
Output reduced by 75% with massive financial and economic benefits
Landfill diversion is a big deal in Vermont, a state that relies on only one landfill. The Bellows Falls Wastewater Treatment Plant is doing its part by diverting virtually all of its waste away from landfills and into more regenerative uses.
Fewer outbound trucks result in lower carbon emissions, and there are also savings on energy consumption due to more energy efficient equipment that may soon include a heat recovery component; in fact, the plant expects to recoup its investment due to energy savings in less than five years. Despite a significant plant expansion, the addition of dewatering and drying technologies, LED lighting improvements and the use of a renewable solar farm have allowed the plant to avoid increases in energy costs.
By removing a greater percentage of water from sludge, Bellows Falls has significantly reduced disposal costs and minimized solids handling challenges, realizing significant operational benefits and an ROI of under five years. Environmental sustainability improvements include keeping more water in the local water system, reduced energy consumption and lower emissions.
Accounting for the challenges faced by the facility, such as aging technology and the installation costs associated with the upgrade, the city’s new screw press and dryer reduced operational costs and man hours and increased environmental benefits while generating much drier solids that do not have to be trucked offsite.
- 75% less solids output
- Virtual elimination of trucking costs and landfill fees
- Dramatically reduced emissions
- Less energy and water consumption
- More water retained in local aquifer
- Creation of Class A biosolids, approved for farmland application