Intellectual Property Initiatives
We must continue to exist to Provide Amenity and Convenience beyond Expectation.
Under our corporate philosophy of “Providing Amenity and Convenience beyond Expectation,” we at AMCON aim to realize a better society by creating products and services that are truly customer-oriented and by providing comfortable and convenient services and products for all facilities in the world.
We strongly feel that our business is indispensable to society and that it is our mission to ensure the company’s continued existence.
Strategies
We are pleased to provide our customers with value-added products protected by intellectual property rights (patent rights, utility model rights, trademark rights, design rights, etc.) so that these products can contribute to our customers and society. Holding intellectual property rights not only in Japan but also in many other countries and regions including China, the EU, the U.S., and India, we are expanding our sales area by providing attractive products and services that earn the trust of customers around the world.
In addition, we respect intellectual property rights held by third parties and recognize that intellectual property rights held by AMCON are important assets, thereby striving to preserve and secure these rights.
Brands
The name given to the first sludge thickener we manufactured and marketed, that is, the word “VOLUTE” meaning “spiral” or “helical”, was designed as a logo and registered as a trademark. The first sludge dewatering press with a made-in-Japan mechanism was developed by AMCON.
It has been 30 years since we started marketing VOLUTE. We have developed a new product that can be used with an even wider range of sludge types. The next generation of VOLUTE products is trademarked as “VOLUTE DUO” due to the characteristics of their mechanism.
Challenge and Creativity as a Manufacturer
AMCON was founded as Environmental Facility Center in 1974.
At that time, our main business was the “maintenance of septic tanks at apartment complexes and sewage treatment plants .”
How did a maintenance company turn into a manufacturer capable of developing its unique sludge dewatering press, VOLUTE™?
As you can see from our motto – “AMCON does it as nobody else will” – we are full of passion when it comes to pioneering the development of innovative dewatering presses. We believe the development of our VOLUTE™ was possible due to our out-of-the-box thinking coupled with a long history of hard work.
How wastewater was treated
in apartment complexes in the 1970s
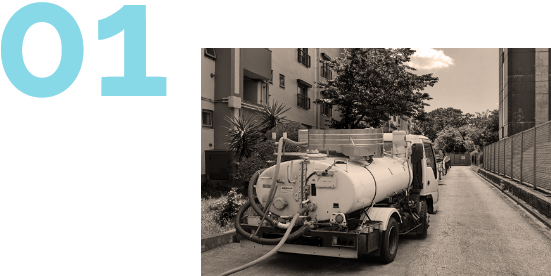
First step – starting as a manufacturer
After extensive research with our development team, in 1982, we finally launched a “sludge thickener using filter cloth” as our first mechanical product. Its small footprint and affordable price satisfied many customers living in apartment complexes.
However, challenges still remained for our first self-developed unit. Separating solids and liquid with a filter cloth was prone to clogging, requiring large amounts of washing water, frequent replacement of filter cloths, intensive labor, and other additional costs. As we were a maintenance company, we were painfully aware of the inconveniences operators went through on site, as such, we felt a duty as a “manufacturer” to resolve the remaining challenges of “labor intensiveness and high operating costs.”
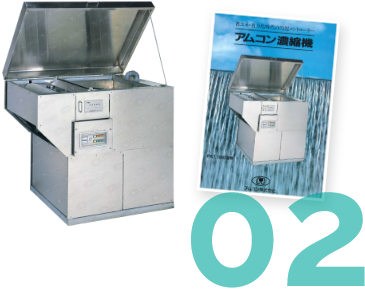
Second step – the birth
of the comb-blade VOLUTE™
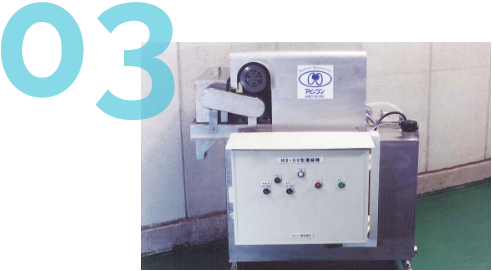
Overcoming the third challenge
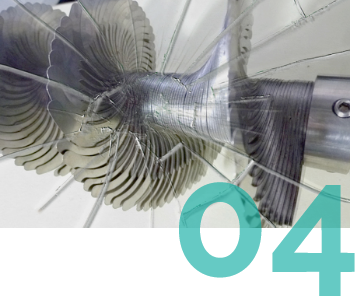
Birth of improved VOLUTE™, eliminating
the need for large amounts of cleaning water
We obtained the second patent in 1992 with this equipment, and it is the origin of the VOLUTE™ Sludge Dewatering Press, which is still one of our core products today.
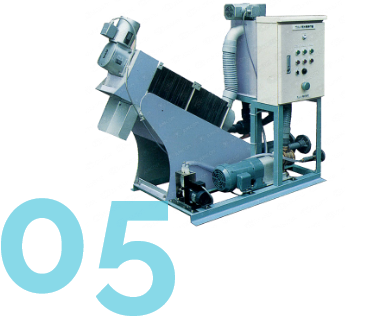
Our never-ending journey
-In 1996, we introduced “Dell Compo,” a sludge dewatering and fermentation system for small WWTPs, realizing “recycling of sludge”;
-In 2004, the “dewatering machine for dry film resist waste” was developed, realizing the dewatering of peeling waste, which is difficult to handle due to its strong alkaline nature;
-In 2016, the “AP series”, a fully automatic polymer make-up unit was developed, realizing an autonomous dissolution process of powdered flocculants;
-In 2018, the “VOLUTE™ DW Series sludge dewatering press” was introduced, enabling stable operation by automating the mechanical response to concentration variations;
-And finally, in 2021, we unveiled the “VOLUTE DUO™ sludge dewatering press,” which can achieve stable dewatering of high fiber / inorganic sludge types.
However, our journey is not over. We will continue to deliver new technologies that provide “amenity and convenience beyond expectation.”
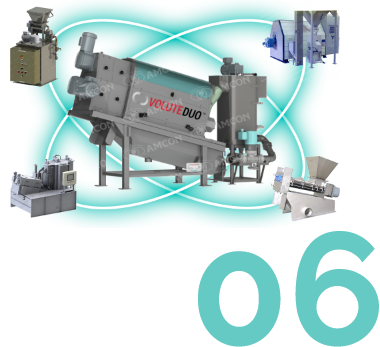
Further challenges and creations with a flexible mindset
With free thinking,
we continue to tackle challenges
and show our creativity.
While our origin was based on maintenance service at WWTP, we have shifted our focus to the development of sludge treatment equipment. That is why we can provide services and products that are close to the feelings of our customers and more specifically the operators who have to deal with sludge daily in the field.
Maintaining the status quo is synonymous with regression.
With an out-of-the-box mindset, we will continue to create products in pursuit of perfection, which is why our engineering journey will never end, leading us to develop even better products for tomorrow.
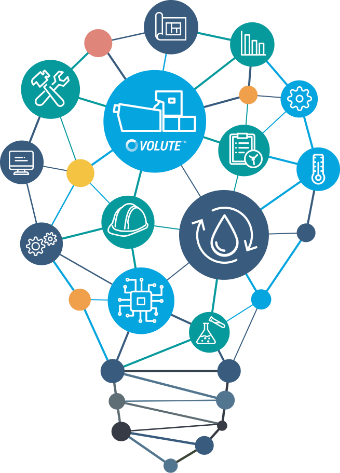